Logistik-Cockpit für das Lager
Ziele
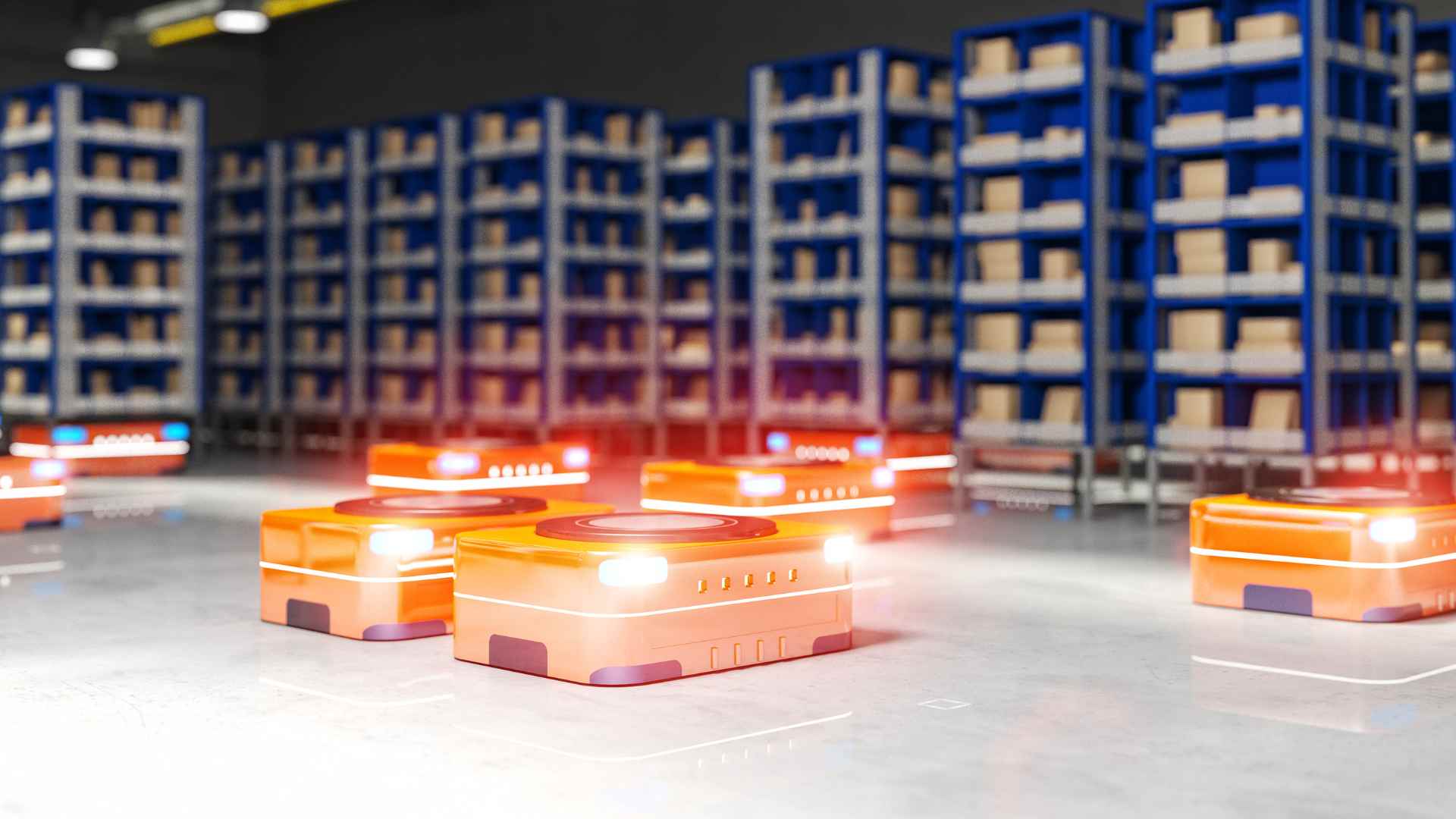
Erstellung eines Logistik-Cockpits zur Optimierung der Lagerung der verschiedenen Bestände und Erstellung eines ABC-Lagersystems.
Ziele
- Bestände über verschiedene Arten an Lägern hinweg tracken
- Platzoptimierung in den einzelnen Lägern
- Strategische Platzierung der Bestände in den passenden Lägern
In Lägern mit mehreren Millionen von einzelnen Beständen ist es eine große Herausforderung den Überblick zu behalten, darüber wo die einzelnen Bestände gelagert werden und ob dies der geeignete Ort für die Lagerung ist.
Bei vielen verschiedenen Lagersystemen, von Schnelldreher in automatischen Kommissionierlager bis hin zu Blockregellagern ist die korrekte Lagerung der Bestände wichtig für eine optimierte Zeit- und Platznutzung.
Die Herausforderung
Bei dem besagten Projekt handelt es sich um ein Lager, das mehrere Millionen von Daten beinhaltet und so das Management und die Optimierung der Situation sehr erschwert wird.
In der bisherigen Situation wurden teilweise Schnelldreher, also kleine einzelne Produkte in großen Blockkegellagern eingelagert, was dazu geführt hat, dass regelmäßig viel Zeit aufgewendet werden musste, um die Produkte weiterzuverarbeiten.
Das Vorgehen
Aus einem selbstgebauten WMS des Kunden werden die Daten extrahiert, bearbeitet und selektiert. Die Daten werden geclustert (von Stundenebene auf Tagesebene), um die Datenmenge zu reduzieren.
Mehrere Millionen an Daten wurden in die Systeme von Baitech Data eingespeist. Dazu gehören auch die Informationen aus den automatischen Kommissionierlager, die im Sekundentakt generiert werden. Die Anzahl der Auslagerungen und die Zeit, die für diese verbraucht werden, werden analysiert, um zu definieren, wo eine Umlagerung zu einem zeitlichen Mehrwert führt und wie hoch dieser Mehrwert ist.
Aus der Datenbasis wird zum einen eine ABC-Kategorisierung des Lagers vorgenommen, um die Bestände optimal einzuteilen. Zum anderen werden die Volumen der verschiedenen Ladungsträger mit den Volumen der einzelnen Produkte verglichen. Zum anderen werden sowohl die Schnelldrehenden als auch die Langsamdrehenden Bestände identifiziert und den entsprechenden Lägern zugeordnet.
Auf diese Weise war es uns möglich viele Lagerplätze zu schaffen durch eine bessere Nutzung der verfügbaren Plätze, ebenso wie eine Zeitersparnis allein für das Auslagern der Bestände von fast 10.000 Stunden im Jahr. Ebenso hat das Unternehmen einen tagesgenauen Überblick über die Bestände und die verschiedenen Bewegungen und Entwicklungen im Lager.