Fallstudien aus der Industrie 4.0
Cloud IdD-Aufzüge
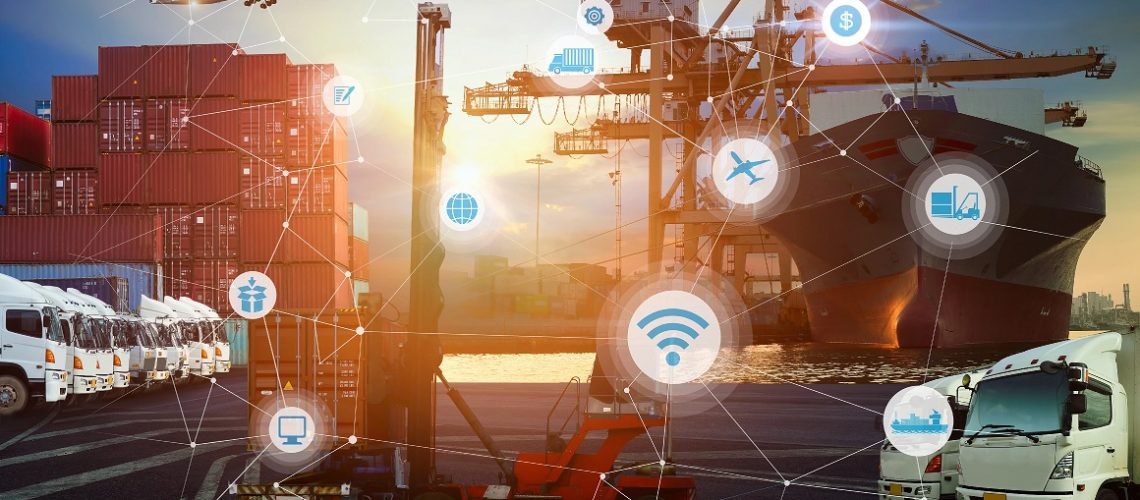
Nachdem die Frage „Was ist Industrie 4.0“ geklärt war, haben wir einige der wichtigsten Aspekte der digitalen Revolution vorgestellt, die Produktionsumgebungen beeinflussen.
Im Folgenden stellen wir Ihnen einige praktische Anwendungen dieser Technologien vor.
Cloud IdD-Aufzüge
Ein auf die Konstruktion und Montage von Aufzügen spezialisiertes Unternehmen hat eine Cloud-basierte Lösung für die prädiktive Wartung in Echtzeit entwickelt.
Dieses Konzept verbindet die Technologien IdD, Cloud, Big Data und künstliche Intelligenz und soll die Ausfallzeiten durch Echtzeit-Diagnosen verkürzen.
Sensoren erfassen Daten wie Türbewegungen, Fahrten, Starts, Anrufe, Fehler etc. und übermitteln diese an die Microsoft-Cloud (Azure). Dort berechnet ein Algorithmus die Nutzlebensdauer der Hauptkomponenten und weist auf Teile hin, die zu überprüfen oder auszutauschen sind. Die Prognose vergleicht die Betriebsvariablen des Aufzugs mit den Daten anderer Anlagen, für die bereits historische Daten vorliegen.
Die Informationen werden an die Wartungsfachkräfte gesendet, damit diese den Zustand jedes Aufzugs in Echtzeit erfahren.
Die Leistungsfähigkeit dieser Lösung basiert auf dem Vergleich der Betriebszustände von tausenden von Anlagen. Aus einer großen Zahl von Fällen lassen sich statistisch aussagekräftige Werte erhalten.
Schätzungen zufolge kann dieses Unternehmen die Stillstände um 50 % verringern. Das senkt die Wartungs- und die damit verbundenen Planungskosten.
Prädiktive Wartung von LIS Solutions
ILIS Solutions hat ein Tool für die prädiktive Wartung der Roboter in den Produktionsanlagen eines bedeutenden Unternehmens im Automobilsektor entwickelt.
Die von den SPS der Roboter der Produktionsanlage übermittelten Daten sowie Daten über Fehler und Vorfälle werden in Datenbanken gespeichert.
Tools des maschinellen Lernens verknüpfen die Vorfälle mit den Betriebsvariablen der Roboter: Drehmoment, Stromverbrauch, Geschwindigkeit und Beschleunigung. Nun lernt der Algorithmus und stellt so die Beziehungen her: Er sucht nach vergangenen Mustern von Werten, die vor einem Fehler auftreten.
Sobald die Alarmwerte identifiziert sind, überwacht das Tool die Roboter der Produktionsanlage kontinuierlich und berechnet für jeden einzelnen die verbleibende Nutzungsdauer (Remaining Useful Life – RUL), das Versagensrisiko (Risk of Failure – ROF) und die Gesamtanlageneffizienz (GAE bzw. Overall Equipment Effectiveness: OEE).
Wenn zum Beispiel ein Roboter zu einer bestimmten Zeit für dieselbe Aufgabe (unter gleichen sonstigen Bedingungen) mehr Strom benötigt, weist das auf eine mögliche Funktionsstörung hin, und das System gibt einen Alarm aus.
Optimierung der ergonomischen Bedingungen der Beschäftigten
In Werken eines Automobilunternehmens in Deutschland erfolgen gewisse Arbeiten aufgrund der kleinen Werkstückgröße und der Eigenschaften dieser Abläufe manuell.
Dieses Werk verfügt über 400 manuelle Arbeitsstationen und beschäftigt rund 350 Mitarbeiter.
Nun lautete das Ziel des Projektes, ein Hilfsmittel zu entwickeln, mit dem die Produktionsleiter die Aufgaben unter Berücksichtigung ihrer Art und Schwierigkeit und der Eigenschaften der betreffenden Person (Alter, Erfahrung, Spezialisierung, körperliche Einschränkungen) und gemäß den Arbeitsschichten aufteilen können.
Bestimmte körperliche Faktoren können die möglichen Tätigkeiten einer Person einschränken. Zum Beispiel kann ein(e) Beschäftigte(r) eventuell nur ein bestimmtes Höchstgewicht heben, den Arm nur bis zu einer bestimmten Höhe strecken und nur eine bestimmte Zeit lang stehen etc.
Durch Verknüpfung der Datenbanken von Arbeitnehmern, Schichten, körperlichen Einschränkungen und mit bestimmten körperlichen Belastungen zu erledigenden Tätigkeiten ließ sich feststellen, welche Tätigkeiten am besten welchen Personen zuzuweisen sind.